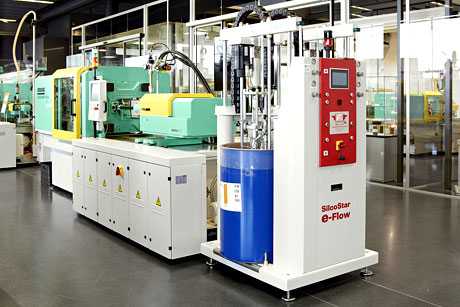
2KM Case Study
2KM stands for 2 Komponenten Maschinenbau, which in English means Two Component Engineering. The company was founded in Germany, in 1976, where two friends partnered up and started building robust and innovative machines to improve existing production processes. 38 years
later, still a family oriented company, they provide solutions worldwide. With five main sites and many distributors globally, we keep expanding while remaining loyal to our values of excellent quality and human approach.
The main operations are based in Marienheide (60km east of Cologne), where 70 members of staff work hard to maintain the quality and performance of the best adhesives metering systems in the market.
The UK operation, 2KM (UK) Limited, was founded in 1998 and is based in Bromsgrove, Worcestershire. It started with a handful of people and has grown significantly through the years. In 2012 new, bigger premises were acquired to accommodate the continuously growing number of projects and team members. The successful gear pump systems Process Gear Mix are now manufactured in the UK. The powerful team of 15 manages
a growing number of customers’ portfolio in almost every market.
Why did 2KM (UK) choose Okappy
2KM looked at a number of different systems. Although not the cheapest, the simplicity and flexibility of the Okappy platform is what sold the solution to Rob McLaren, Managing Director of 2KM (UK) Limited.
How are 2KM using Okappy to streamline their business and reduce costs
2KM uses Okappy from the very earliest stages of their process. Their sales force log jobs on to the system when they first meet a new prospect. They can store information related to that prospect and keep the office updated in real-time.
Once the prospect has been converted into an actual customer, then additional jobs can be added such as installation of machines or service and maintenance jobs.
The jobs are allocated to the engineer who may have to travel anywhere around Europe, Middle East and Africa. They get the information on their phone or tablet and update the job once it’s done. This information is available immediately back in the office.
How has this benefited 2KM
Information is more readily accessible.
Engineers can see the information without having to come back to the office to pick up job sheets. Machine schematics can also be saved with the job to aide in maintenance. Previous visit information is also available including photos or other attachments which means they are more likely to be able to fix or service the machines on the first visit, saving time and money.